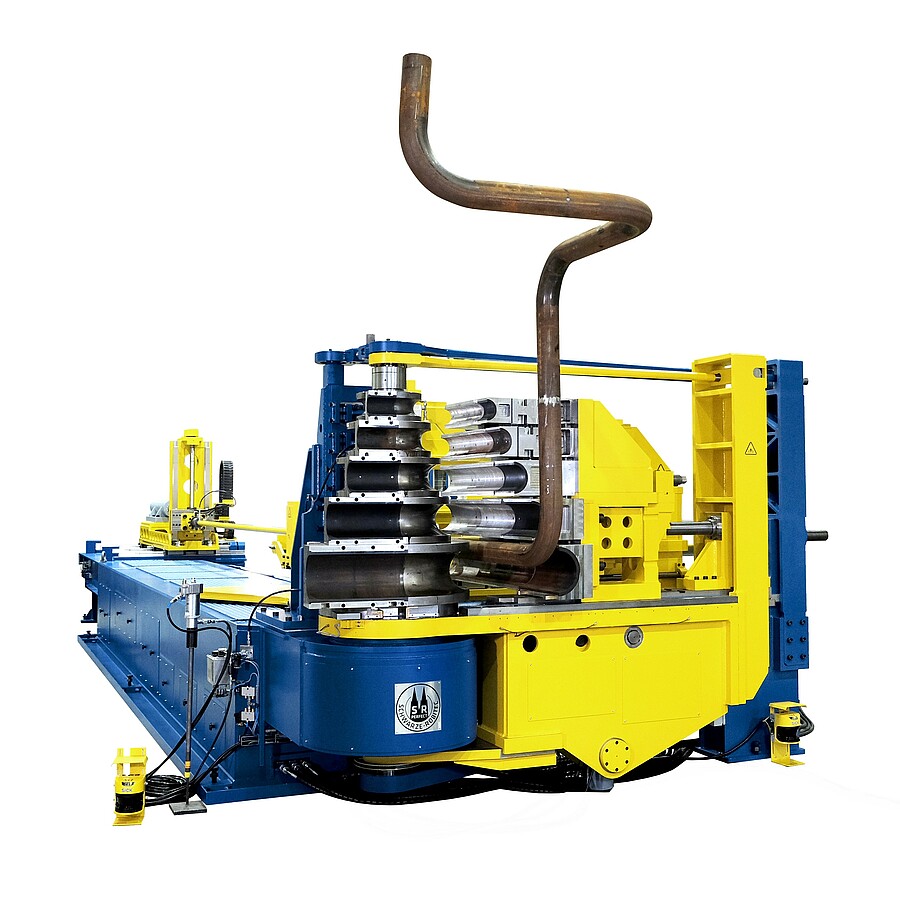
Thanks to Schwarze-Robitec on the oceans of the world
Bending without changing tools: Two new machines for Meyer Werft
Around 400 kilometers of tube, 52,000 individual pieces, are installed in a single cruise ship: This is the sheer quantity that the Meyer Werft tube center manufactures for every ship that Meyer Werft in Papenburg launches. The German shipbuilder is once again relying on two new machines from Schwarze-Robitec. They ensure fast, safe and high-quality processing of tubes of various dimensions due to the use of multi-stack tooling, which eliminates a major part of the time-consuming tool change process.
“Made in Germany”, the cruise ships and ferries of Meyer Werft set sail on all the world’s oceans. For more than 17 years, the Papenburg shipbuilder has relied on the tube bending machines from Schwarze-Robitec, which are also manufactured in Germany. Now, the Cologne-based tube bending expert has put two new machines into operation at Meyer Werft: A CNC 100 HD MW bends steel and stainless steel tubes with diameters ranging from 42.2 mm to 88.9 mm, while a CNC 220 HD MW handles the 114 mm to 219 mm range. Both machines are equipped with a so-called five-stack tool tower in the respective diameter range, which allows the majority of the tools to remain set up simultaneously thanks to the multi-level tool design. Tubes of different diameters and wall thicknesses can thus be bent without changing tools. Components such as the pressure die and clamping jaws as well as the massive bending former are very large and heavy for the tubes to be produced in shipbuilding. Changing by crane costs time and energy and involves quality risks for the result, as the tool has to be readjusted each time. Only the bending mandrel and the collet inserts in the index head have to be changed by the Meyer Werft tube center for a different tube size. Meyer Werft benefits from enormous setup time savings and a steady, consistently high-quality bending result.
Schwarze-Robitec also supplied a semi-automatic loading device for each machine: A magazine separates tubes on manual request, which are then transferred to a loading table. This height-adjustable table transports the tube to the appropriate loading height, where it is fed into the machine’s index head for the subsequent bending process. This simplifies the otherwise sometimes dangerous process even more and represents a high safety factor for Meyer Werft, because loading tubes of such length and weighing several 100 kilos can otherwise only be achieved with the help of a crane and a balanced suspension at two points.
Two comparable machines from Schwarze-Robitec had already been in operation at Meyer Werft Rohrzentrum since 2004 but have now been relocated to another site. They are replaced in Papenburg by the new models, which are state of the art with further developed control and operation – for many more ships to be launched in Germany.